Alongside with series-produced equipment, one of the main activities of our company is designing and manufacture of line for profile production based on the customer’s drawings. Highly skilled professionals develop and manufacture the equipment. Creating the machines, the company’s developers calculate the minimum number of passes for obtaining high-quality products and optimize the roll formers machine design.
Based on the material, workpiece thickness and finished profile configuration, and to minimize the designed specific quantity of metal directly influencing both the machine cost and the manufactured product cost, three different element bases are used for the machine manufacture:
Light – production of simple profile configuration, 1,0 to 1,2 mm thickness.
Heavy - (heavy-duty bearing supports, shafts, sprockets and a frame, a more powerful electric drive) - manufacture of shapes of a more complex configuration, up to 2.0 mm thickness.
Adjustable width – profile production of simple configuration with changeable width, up to 0,5-0,7 mm thickness. When the handwheel is rotated using two screw pairs, the movable carriers with shaping rollers move synchronically.
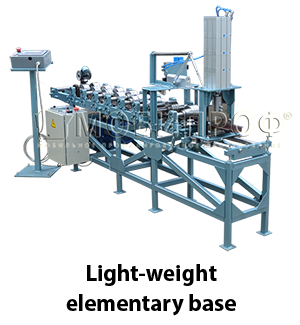
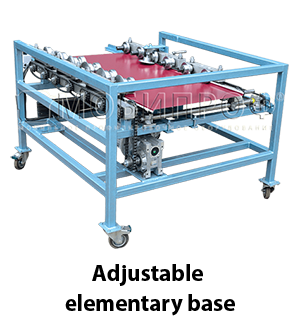
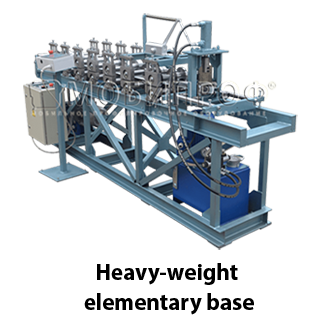
Our machines operate with both required width blanks preliminarily cut into specific cut length flats, and rolls (strip). When using the preliminarily prepared specific cut length blanks, only shaping machine is required for the shape rolling.
When operating from the roll, the equipment is optionally equipped with profile pneumatic (up to 0,7-1,0 mm) or hydraulic (up to 2,0 mm) guillotine for cutting the finished shape at the machine outlet, and numeric control system (CNC) for synchronization of operation of the machine and guillotine.
Depending on the profile configuration, stationary or flying cut can be implemented (without shaping process stop). The automated control system is equipped with an operator touchpad which facilitates the parameter entry and monitoring process, and enables entering 10 different modes into the system memory. The equipment can be additionally equipped with devices for chipping, cutting-out or hole punching.
When rolling shapes from workpiece of the required width and length the guillotine and CNC are unnecessary, which reduces not only the equipment cost, but also the equipment capacity. When working with coiled strip, the operator engages the flat, sets the operation mode (length, quantity of items and speed). “The flying cut” device allows increasing capacity by 45-50% as compared with stationary cut and by 90-100% as compared with a machine without guillotine, thus decreasing the produced shape cost.
When rolling shapes with workpiece at the shape ends, at shape start and end positions, there is a 5 to 15 cm area where there occurs “opening” process, i.e. 2-3° angle mismatch. Its decrease (but not total elimination) is possible if a profile guillotine is installed at the machine outlet.
To calculate the equipment cost, it is necessary to send a shape drawing or sketch to our e-mail address: info@mobiprof.ru indicating your contact details.